After a long day at the pool or a serious training session, the last thing you want is discomfort or foggy vision caused by poor-quality goggles. That’s where the true craftsmanship behind every pair of goggles comes into play. Behind the scenes, swimming goggles are made in high-tech facilities like a swimming goggles factory, where precision and innovation are key to delivering top-tier products. Let’s dive into the fascinating process of how swimming goggles are made, from start to finish.
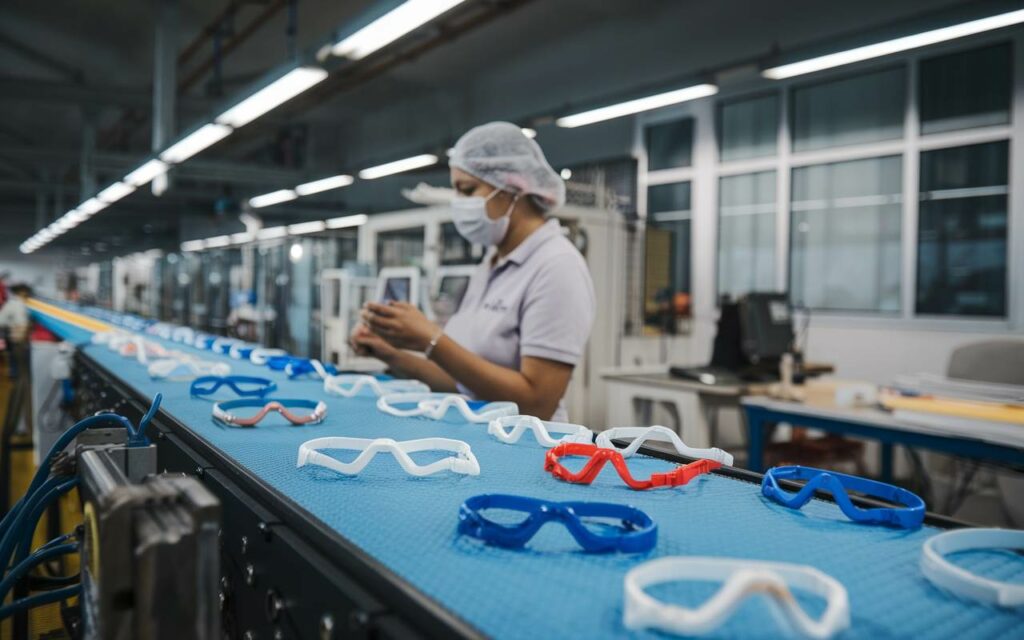
What Material Are Swimming Goggles Made Of?
Swimming goggles are crafted from a combination of materials chosen for their flexibility, durability, and resistance to the harsh conditions of chlorinated water. The primary components of swimming goggles include silicone, polycarbonate, and thermoplastic elastomers (TPE). The lenses, typically made from polycarbonate, are lightweight, scratch-resistant, and offer excellent optical clarity. Silicone, known for its softness and flexibility, is commonly used for the seals and straps, ensuring a comfortable and water-tight fit. In many swimming goggles factories, these materials ensure a balanced blend of comfort, performance, and longevity, creating a product that meets the needs of swimmers at all levels.
Manufacturing Process in Swimming Goggles Factory
The journey of crafting high-quality swimming goggles begins with precise planning and innovative techniques. At Vanguard, a leading swimming goggles in Chinese factory, each step is meticulously designed to ensure optimal performance and comfort. Here’s their manufacturing process.
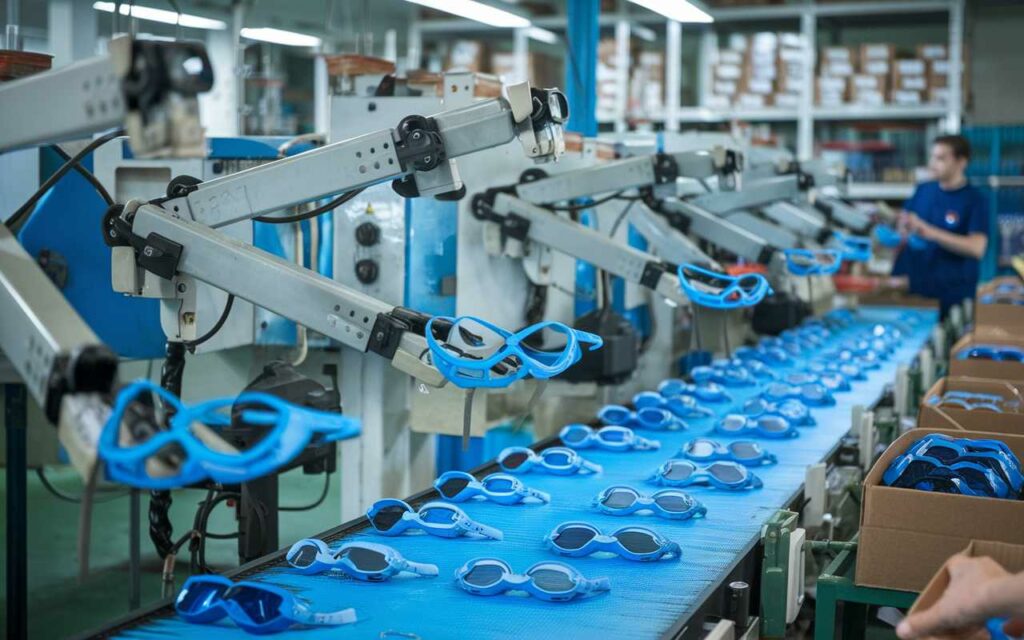
Raw Material Inspection
Before production begins, a thorough inspection of all incoming raw materials is performed. This includes checking the quality of silicone, polycarbonate, and other materials used in manufacturing swimming goggles.
- For silicone, specifications ensure it is soft, flexible, and hypoallergenic, allowing for a comfortable, secure fit without irritating the skin.
- Polycarbonate lenses are carefully examined for optical clarity, scratch resistance, and impact durability to withstand water pressure and rough handling.
- Other materials, such as thermoplastic elastomers (TPE) for the frame, must meet specific durability and flexibility standards.
Only when these materials meet strict specifications do they proceed to the next stage of production and ensure the final product is both durable and comfortable.
Design and Prototype
Once the raw materials are approved, the next step is bringing the vision of the swimming goggles to life through design and prototyping. This stage is where creativity meets engineering, ensuring that every aspect of the goggles, from fit to functionality, is refined before mass production begins. Let’s break down the key steps in this critical phase:
- Concept Creation: Designers begin by developing an initial concept based on market needs and performance goals. This involves determining the type of swimmer the goggles are for—professional athletes, casual swimmers, or recreational users—and incorporating design elements that enhance comfort, aerodynamics, and clarity.
- 3D Modeling: Once the concept is finalized, designers use advanced 3D modeling software to create a virtual representation of the goggles. This allows them to simulate how the design will look and function, and make adjustments to factors like lens curvature, frame fit, and strap placement, all while ensuring the design meets both aesthetic and functional standards.
- Prototype Testing: After the 3D model is completed, a physical prototype is produced using rapid prototyping techniques such as 3D printing. The prototype undergoes extensive testing to evaluate its fit, comfort, and overall performance. This is a crucial stage where real-world feedback helps identify areas for improvement before proceeding to mass production.
Mold the Lens and Frame
With the design finalized and the prototype tested, the next step in the process is molding the lens and frame. This stage involves precision manufacturing techniques to ensure that both the lenses and the frame meet the required specifications for durability, fit, and functionality. Here’s how it unfolds:
- Lens Molding: Polycarbonate, known for its strength and clarity, is used to create the lenses. The material is heated and injected into specially designed molds, where it takes on the precise curvature needed for optimal underwater vision. The molding process ensures each lens is uniform in shape and free from imperfections, providing swimmers with clear, undistorted vision.
- Frame Molding: The frame, typically made from flexible thermoplastic materials, is molded in tandem with the lenses. This step involves injecting the material into molds to form the exact shape and size required for the goggle’s structure. Precision is essential to ensure that the frame holds the lenses securely while maintaining a comfortable fit around the swimmer’s face.
- Curing and Cooling: After molding, both the lenses and the frame undergo a curing process. This step involves heating the materials to a specific temperature to harden them and increase their durability. Once cured, the components are carefully cooled, allowing the materials to solidify and retain their shape, ensuring the final product’s strength and resilience against water pressure and everyday wear.
Assemble the Goggle Parts
Once the lens and frame are molded and cured, the next step in the process is assembly. This stage brings together all the individual components to create a fully functional pair of swimming goggles. Precision is crucial to ensure that each part fits seamlessly and performs at its best. Here’s a breakdown of the assembly process:
- Lens Attachment: The first step in assembly is attaching the molded lenses to the frame. This is a delicate process, as the lenses must fit securely into the frame without shifting or leaking. High-quality adhesives or locking mechanisms are used to ensure a tight, water-resistant seal, preventing any discomfort or vision impairment during use.
- Seal Installation: Next, soft, flexible silicone seals are carefully installed around the lenses. These seals form a watertight barrier against the swimmer’s face, preventing water from seeping into the goggles. The seals also add comfort by cushioning the frame, reducing the pressure on the face and creating a snug, secure fit.
- Strap and Nose Bridge Assembly: The final assembly step involves adding the adjustable strap and nose bridge. The strap, made of durable silicone or rubber, is attached to the frame to ensure a secure fit around the swimmer’s head. The nose bridge, which is often adjustable, ensures that the goggles sit comfortably on different face shapes without pinching or causing discomfort. With these parts assembled, the goggles are nearly ready for testing and final adjustments.
Test for Quality Control
Before the swimming goggles are ready for packaging and shipment, they undergo a rigorous quality control process to ensure they meet the highest standards of performance and durability. Each test is designed to simulate real-world conditions and identify any potential flaws. Here’s an overview of the key quality control tests:
- Leak Test: One of the most critical tests, the leak test ensures that no water can seep into the goggles during use. Each pair is subjected to a water immersion test to check the integrity of the seals and the lens attachment. If any leaks are detected, the goggles are sent back for adjustments to ensure a perfect fit and water-tight seal.
- Impact Resistance Test: Swimming goggles need to withstand accidental drops and rough handling. To assess the durability of the lenses and frame, the goggles undergo an impact resistance test. This involves dropping them from a specified height onto a hard surface to ensure they don’t crack, shatter, or lose their shape. This ensures that the goggles are durable enough for daily use.
- Anti-Fog Coating Application: To improve visibility and comfort, an anti-fog coating is applied to the interior surface of the lenses. This coating prevents condensation from forming during use, ensuring swimmers can maintain clear vision throughout their swim. After application, the goggles are tested for effectiveness to ensure the coating lasts and performs as expected.
- Fit Testing: The final quality check involves testing the fit of the goggles on a variety of face shapes and sizes. This step ensures that the goggles provide a snug, comfortable fit, with the seals resting properly on the skin without causing discomfort. The fit testing also includes checking the adjustability of the strap and nose bridge to accommodate different head sizes. Once they pass all these tests, the goggles are ready for packaging and shipping.
Package and Labeling
After passing all quality control tests, the finished swimming goggles are carefully packaged and labeled. Each pair is carefully placed in protective packaging to avoid damage during transportation. The labeling includes important information, such as product specifications and instructions for use, along with branding and other relevant details. For swimming goggles wholesale, this packaging process is essential for ensuring that the goggles reach their destination in perfect condition.
Technology and Innovations in Goggle Manufacturing
The world of swimming goggles has evolved dramatically in recent years, thanks to technological advancements and innovative manufacturing techniques. As demand for higher-quality, performance-oriented goggles grows, manufacturers are continuously pushing the boundaries of design and functionality. Here’s a look at some of the key technologies and innovations shaping the future of goggle manufacturing:
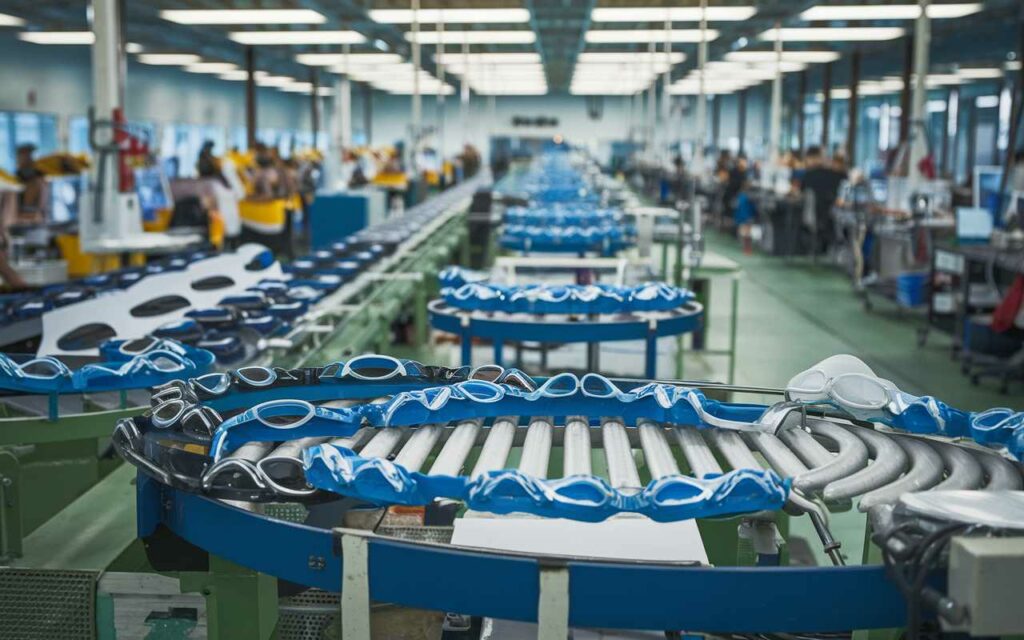
- Advanced Lens Technology: Modern swimming goggles are now equipped with lenses designed to provide superior optical clarity and reduced glare. Innovations in lens coatings, such as anti-scratch, anti-fog, and UV-protection coatings, have become standard in high-end goggles. These coatings are applied using advanced techniques like vacuum deposition, ensuring durability and effectiveness.
- Hydrodynamic Design: To improve speed and reduce drag, the design of swimming goggles has become more aerodynamically refined. Manufacturers are utilizing fluid dynamics simulations to create goggle shapes that enhance performance by minimizing resistance in the water. This has led to the development of more streamlined goggles, especially for competitive swimmers.
- Smart Goggles: In recent years, swimming goggles have begun incorporating smart technology, such as built-in displays that show real-time data like lap times, stroke count, and heart rate. These innovations, made possible by miniaturized sensors and advanced display technology, cater to professional athletes and tech-savvy swimmers who want to monitor their performance in the pool.
- Customizable Fit: The demand for greater comfort has led to the development of goggles with customizable features, such as adjustable nose bridges and straps made from flexible, soft materials like silicone. Some companies are even offering 3D-printed goggles tailored to the swimmer’s unique facial contours, improving both comfort and water-tightness.
- Sustainability and Eco-Friendly Materials: As environmental concerns grow, many manufacturers are turning to sustainable practices in goggle production. This includes using recycled or bio-based materials for frames and straps, as well as packaging solutions that minimize waste. These innovations help reduce the environmental impact of manufacturing while still maintaining the high standards expected by consumers.
Conclusion
From the careful selection of materials to the precision testing in a swimming goggles factory, every step in the production of swimming goggles ensures a product that meets the highest standards. Whether aiming for a competitive edge or simply want a comfortable swim, understanding this process enhances your appreciation for the quality and technique behind your goggles. Ready to choose the best for your next swim? Check out our selection of premium goggles today.